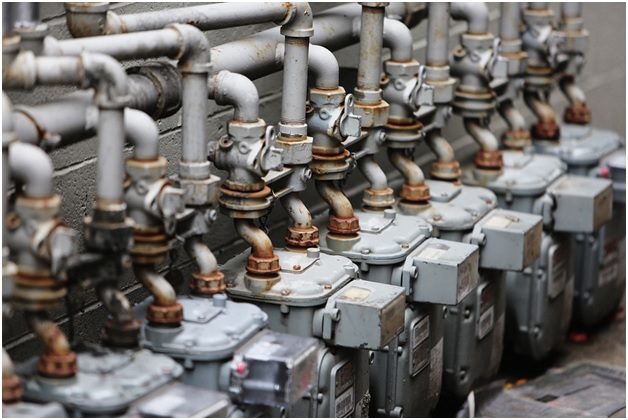
Industrial valves do come in different shapes, sizes, and serve different purposes. For multiple types of industries and applications, multiple valves are also being used.
When talking about types of directional control valves, the variations range from basic to advance. Other valves are complicated enough to automatically adjust to temperature and pressure. However, regardless of how they are being constructed, flow control valves are made to adjust the pressure and flow of fluids. They often react to signals made by temperature or meter flow.
Since industrial valves are used in various industry settings, let’s get to know the most commonly used flow control valves in different industries today and what are their functions. For industrial raw materials, you can check out Taiangreenindustry.
Globe Valves
Globe valve is a type of linear motion valve that regulates fluid flow. Globe valves manage the closing process through a plug with a convex bottom that is positioned lower in a horizontal seat. They are often placed in the center of the valve. When you open it, the plug raises to let the fluid flows. Moreover, globe valves are used for turning on and off as well as throttling procedures since the disk can be removed entirely from the flow path.
While globe valves can produce a bit of higher pressure drops compared to other valves, they are applicable in different processes where the pressure drop is not a controlling element.
Gate Valves
When it comes to general services valves used for on/off procedures and non-throttling applications, gate valves are the best choice. They are specifically used in procedures that need a straight-line fluid flow with less restriction. Gate valves operate when you rotate the stem in a clockwise pattern to close and open.
Gate valves maneuver up or down when you move the stem on a threaded step. This is the exact reason why they are multi-turn valves. To prevent the water hammer effect, the valves must turn several times for them to open and close. Most engineers make use of gate valves when there is less pressure loss. The usual gate valves have zero obstruction in the pathway flow, which relatively leads to minimal loss of pressure.
They are also used for multiple fluids and are generally applicable for wastewater, water, and neutral liquids under a temperature that ranges from 20 – 70 degrees.
In addition, there are two major gate valve types — wedge-shaped and parallel. Wedge-shaped gate valves consist of two seats and gate that are slightly mismatched. While parallel gate valves are comprised of a flat gate between two seats parallel to each other.
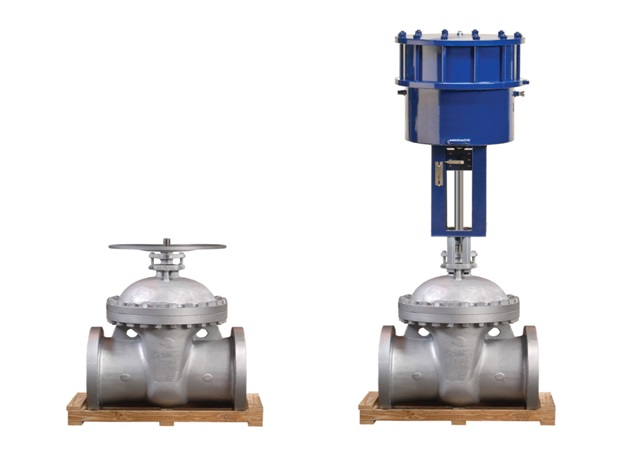
Needle Volume Control Valves
These type of valves restrict fluid flow in small lines. Fluid coming through the valve shifts 90 degrees and flows through an open orifice. The orifice acts as the seat for a cone-shaped rod. The size of the orifice varies when you place the cone in relation to the seat panel. Needle valves are the same to globe valves because of their design features and benefits. Both have operators to change the flow rate.
However, the difference between them is that needle valves can achieve great precision. As a matter of fact, they are highly recommended for calibration procedures since they can be fine-tuned. Needle valves can positively shut off for gauges and other instruments for measurement to be safely removed or applied.
The same reason why most industries use needle valves, from petrochemicals to biofuels. One of the unique features of needle valves is its finely-threaded valve stem. It gives a mechanical advantage by granting you to cover it using less energy force. However, one disadvantage of needle valves is that it is not enough to have visual inspection alone to see if the valve is closed or open.
Diaphragm Valves
Another most commonly used flow control valve are diaphragm valves. They are identified by pliable discs that connect the topmost seat of the valve and create a seal. Diaphragm valves are pretty much flexible and are responsive to pressure. They deliver force to open, close, or manage a valve during applications. These valves are related to pinch valves and are using elastomeric diaphragm instead of elastomeric liner in the body of a valve.
Diaphragm valves are best for managing corrosive because of its elastomeric feature attached to a compressor. This will then separate the flow stream from the sealing element. There are a lot of advantages to utilizing diaphragm valves, such as they are super clean, they have a leak-proof seal, they are easy to maintain, and best of all, they help reduce leakage that might affect the environment.
These valves can be repaired without getting or touching the pipeline. However, just like with other valves, diaphragm valves also have their disadvantages — using them should be under a moderate temperature (-60 to 450 degrees Fahrenheit) and must be in moderate pressures of 300 psi.
They cannot be utilized in different operations and zero standards in terms of face-to-face dimensions. Moreover, diaphragm valves must have a body made of materials that are resistant to corrosion.
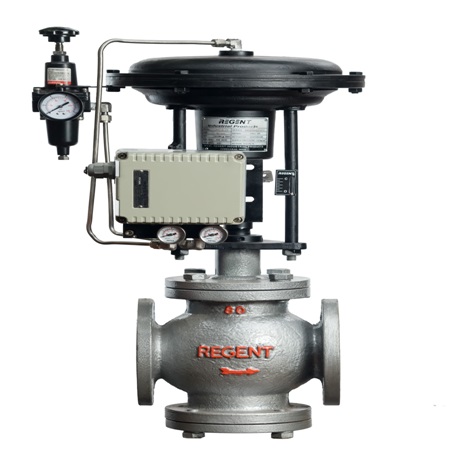
Pinch Control Valves
Pinch control valves are best for applications of liquids containing suspended solids. These valves are used to seal one or more malleable elements, such as rubber tubes, polyvinyl chloride, etc.
Hydraulic or air pressure is assembled on the elastomer sleeve directly, this is to actuate pinch valves. The body of pinch valves serves as built-in roller screw actuator, which removes expensive pneumatic, electric, or hydraulic operators. This will then result in the cost-effectiveness of pinch control valves to the industry.
Conclusion
It’s best that you have an idea about the commonly used valve types on the market. This way, it will be easier for you to determine which or what type to use depending on your applications. Keep in mind that some industrial valves may some time look a bit the same, however, each has its respective purpose and use.